The Double Roller Fertilizer Production Line is an advanced and efficient solution in the fertilizer manufacturing industry. This system is designed to meet the increasing demand for high-quality granulated fertilizers, particularly for compounds like NPK and other specialty fertilizers. By utilizing the principles of roller compaction and granulation, the double roller fertilizer production line offers a cost-effective and environmentally friendly solution for fertilizer manufacturers worldwide.
In this article, we’ll explore the key features, benefits, and working processes of the Double Roller Fertilizer Production Line, as well as how it contributes to the overall efficiency of fertilizer production.
What is a Double Roller Fertilizer Production Line?
A Double Roller Fertilizer Production Line is a type of granulation equipment used in the production of granular fertilizers. Unlike traditional methods of granulation, such as rotary drum granulation or pan granulation, the double roller system uses two counter-rotating rollers to compress the raw materials into granules. These rollers are equipped with specific patterns or indentations that allow the material to be compacted and formed into granular shapes.
This technology is typically used for producing compound fertilizers, such as NPK fertilizers, where different nutrient elements are combined into a single granule. It is also applicable for producing organic fertilizers and other specialty fertilizers. The granules produced by the double roller press are uniform in size, ensuring even nutrient distribution when applied to crops.
Key Features of the Double Roller Fertilizer Production Line
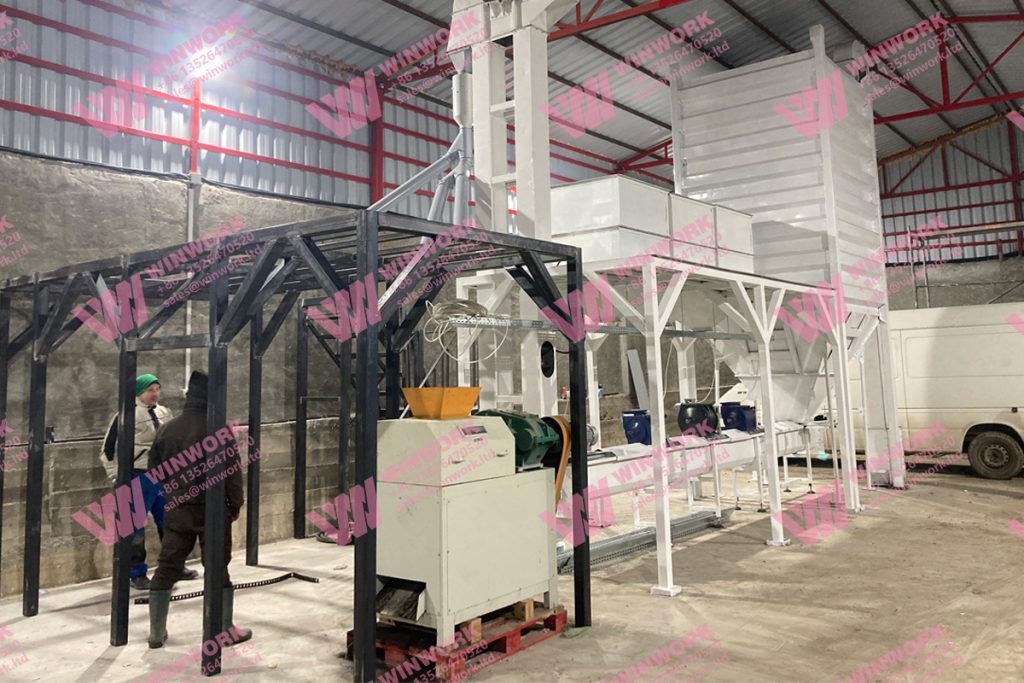
Small scale npk fertilizer production line
a. High-Quality Granulation
The Double Roller Fertilizer Production Line is known for its ability to produce high-quality granules with uniform size and shape. The granulation process uses the principle of roller compaction to form fertilizers without the need for heat, making it energy-efficient and reducing the risk of nutrient degradation. This results in granular fertilizers that dissolve and release their nutrients slowly and steadily, which is ideal for crops requiring a consistent supply of nutrients.
b. Energy-Efficiency
Compared to traditional granulation methods like rotary drum granulation, the Double Roller Fertilizer Production Line consumes less energy. The absence of heat in the process minimizes energy costs and reduces the environmental footprint of production. The system’s compact design also ensures that it takes up less space, making it suitable for operations with limited space.
c. Versatility in Fertilizer Production
This production line is highly versatile and can be used for manufacturing various types of fertilizers, including NPK fertilizers, organic fertilizers, and compound fertilizers. It is particularly effective for producing granular fertilizers with a consistent size distribution, which ensures uniform application in fields.
Moreover, the line is compatible with different raw materials, such as animal manure, plant residues, and chemical compounds. This versatility makes the double roller production line a go-to choice for manufacturers looking to diversify their product range and cater to different agricultural needs.
d. Low Operating Costs
The Double Roller Fertilizer Production Line is known for its low operating costs due to its simple design and minimal need for consumables. The equipment is built to be durable and requires less maintenance compared to other granulation machines. Its straightforward operation also reduces the need for skilled labor, making it a cost-effective solution for fertilizer manufacturers.
Working Process of the Double Roller Fertilizer Production Line
a. Preparation of Raw Materials
The first step in the production process is preparing the raw materials. This typically involves mixing different nutrient sources (such as nitrogen, phosphorus, and potassium) into a homogeneous blend. Depending on the type of fertilizer being produced, additional ingredients like trace minerals or organic additives may also be included.
b. Feeding and Compaction
Once the raw materials are prepared, they are fed into the double roller compaction unit. The two counter-rotating rollers apply pressure to the raw material, compacting it into dense sheets. These sheets are then broken down into smaller pieces or granules by the roller indentations. The pressure and speed of the rollers can be adjusted based on the material being processed and the desired granule size.
c. Granulation and Sizing
After the material is compacted and granulated, the next step is sizing. The granules are sieved to ensure that only those of the correct size are selected for further processing. Granules that are too large or too small are sent back for reprocessing to ensure uniformity in the final product.
d. Cooling and Drying
Once the granules are formed, they undergo a cooling process. This helps solidify the granules and prevent them from sticking together. Cooling also ensures that the granules maintain their integrity during storage and transportation. Depending on the moisture content of the granules, a drying process may also be required to ensure optimal storage conditions.
e. Packaging
After the granules have been properly cooled and dried, they are ready for packaging. The final product is typically packaged in bags or bulk containers for distribution to agricultural customers. Packaging ensures that the fertilizer is protected from contamination and moisture, preserving its quality during storage.
Benefits of Using the Double Roller Fertilizer Production Line
a. High Granulation Efficiency
One of the biggest advantages of the Double Roller Fertilizer Production Line is its high granulation efficiency. The machine ensures uniform granules with a consistent size distribution, which improves the effectiveness of the fertilizer application. The uniform granules also lead to more efficient nutrient absorption by plants, reducing waste and maximizing crop yields.
b. Environmentally Friendly
The use of roller compaction eliminates the need for high temperatures, making the production process more energy-efficient and environmentally friendly. This also reduces the risk of nutrient loss due to heat exposure. The energy-efficient nature of the machine helps lower production costs, making it an appealing option for manufacturers seeking to reduce their environmental footprint.
c. Improved Fertilizer Performance
The granules produced by the Double Roller Fertilizer Production Line have excellent flow properties, which makes them easier to handle and apply. These properties ensure that the fertilizer is applied evenly, reducing wastage and promoting better growth in crops.
d. Minimal Dust and Pollution
Since the production process involves compaction rather than heat, there is minimal dust generation. This reduces the need for dust control systems and contributes to a cleaner working environment.
Conclusion
The Double Roller Fertilizer Production Line is an advanced and efficient solution for manufacturers looking to produce high-quality, granular fertilizers. Its energy-efficient design, ability to handle a wide range of raw materials, and consistent granulation quality make it an ideal choice for producing NPK fertilizers, organic fertilizers, and other compound fertilizers.
This production line not only offers significant cost savings and operational efficiencies but also contributes to a more sustainable and eco-friendly fertilizer production process. As the demand for high-quality fertilizers continues to rise globally, the Double Roller Fertilizer Production Line stands out as a cutting-edge solution for modern fertilizer manufacturing.
Get A Quote