Commonly used raw materials for cat litter production line:
Bentonite ore, adhesive, silica gel, waste paper, pulp, wood chips, sawdust, tapioca, deodorant, tofu dregs, corn starch and so on.
Cat litter production line process
1. Cat litter production line Preparation of raw materials
Bentonite cat litter and agglomerated cat litter:
Working Principle: Bentonite ore is transported to the production plant after mining, and after preliminary screening and decontamination to remove large stones and impurities.
Process Description: The raw ore is screened using a vibratory screening machine to ensure the removal of large lumps, making subsequent processing more uniform and efficient.
Crystal Cat Litter:
Working Principle: Use high quality silica gel raw material for initial screening to remove impurities.
Process description: Use the tumbler sieving machine to sieve out the large impurities and irregular particles in the silica gel particles to ensure uniform particles.
Paper cat litter and wood cat litter:
Principle of operation: Waste paper or wood shavings are collected and fed to the production line for initial shredding and drying.
Process description: Waste paper is cut into small pieces using industrial shredders or wood chips are crushed into small particles for subsequent processing. The chips are then dried in a rotary dryer.
2. Cat litter production line Crushing and sieving
Bentonite cat litter and agglomerated cat litter:
Principle of operation: The bentonite ore is crushed into small particles by means of a crusher and screened to ensure uniform particle size.
Process description: Initial crushing is carried out using a jaw crusher to break large bentonite ores into smaller pieces. This is followed by further crushing with a cone crusher to achieve the required particle size. Finally, it is screened by vibrating sifter to ensure uniform particles.
Crystal Cat Litter:
Working Principle: Silica gel particles are sieved using a tumbler sifter to remove oversized or undersized particles.
Process Description: The silica gel particles are screened through the tumbler sifter, the oversized particles are returned to the crushing process, and the oversized particles go into the waste treatment system to ensure that the final product particles are uniform in size.
Paper Litter and Wooden Litter:
Principle of operation: Waste paper or wood shavings are shredded into uniform particles using a shredder and screened.
Process description: Paper is cut into small pieces by a shredder and wood chips are crushed into small particles by a pulverizer. Subsequently, the particles are sieved through a vibratory sifter to ensure uniformity of size.
3. Cat litter production line Drying
Bentonite cat litter and agglomerated cat litter:
Principle of operation: The crushed and screened bentonite particles are dried in a rotary dryer to remove excess moisture.
Process description: Bentonite particles into the rotary dryer, the dryer through the rotation and hot air system to evaporate the moisture in the particles. The drying temperature is controlled at 100-150°C and the drying time is 2-3 hours.
Crystal Cat Litter:
Working Principle: Drying of silica gel pellets using a tumble dryer to ensure the moisture absorption of the pellets.
Process description: Silica gel particles enter into the drum dryer, which evaporates the water in the particles through the low-temperature hot air system. The drying temperature is controlled at 80-100°C and the drying time is 1-2 hours.
Paper cat litter and wood cat litter:
Principle of operation: The paper or wood pellets are dried by rotary dryer after shredding and sieving to remove excess moisture.
Description of the process: The paper or wood pellets enter the rotary dryer, which evaporates the water in the pellets by means of a rotating and hot air system. The drying temperature is controlled at 80-120°C and the drying time is 1-2 hours. 4.
4. Cat litter production line Pelletizing (applicable to agglomerated cat litter and part of paper and wood cat litter)
Agglomerated cat litter:
Working principle: through the roller granulator or disk granulator bentonite particles pressed into a ball, to enhance the agglomeration performance.
Process description: bentonite particles into the extrusion pelletizer, through the screw extrusion and blade cutting to form uniform spherical particles, or through the disk pelletizer rotation and rolling to form spherical particles. The diameter of pellets after pelletizing is usually 3-8 mm.
Paper cat litter and wood cat litter:
Principle of operation: Paper or wood pellets are pressed into columns using roll granulators, flat die granulators or ring die granulators to enhance hygroscopic properties.
Process description: After the material enters the granulator through the inlet, it is squeezed under high pressure into the holes of the rollers, flat dies or ring dies to form columnar particles. Subsequently, these granules are cut into uniform lengths, usually 2-5 mm, by the cutting knives and finally discharged from the discharge opening.
5. Cat litter production line Cooling
The dry pellets are cooled to room temperature by means of a rotary cooler or an air cooling system.
Cat litter production line Description of the process: The dried pellets are fed into a rotary cooler, which cools the pellets to room temperature (approx. 20-25°C) by means of a rotating and cold air system, ensuring that the pellets are not subjected to thermal stresses.
6.Cat litter production line Packaging
The cooled pellets enter the automatic packing machine through the conveyor belt, the packing machine weighs the pellets and loads them into the preset bags. Finally, the bags are sealed by a heat sealer to ensure that the product is hermetically sealed and moisture-proof. The weight of the bag is usually 5kg, 10kg or 20kg.
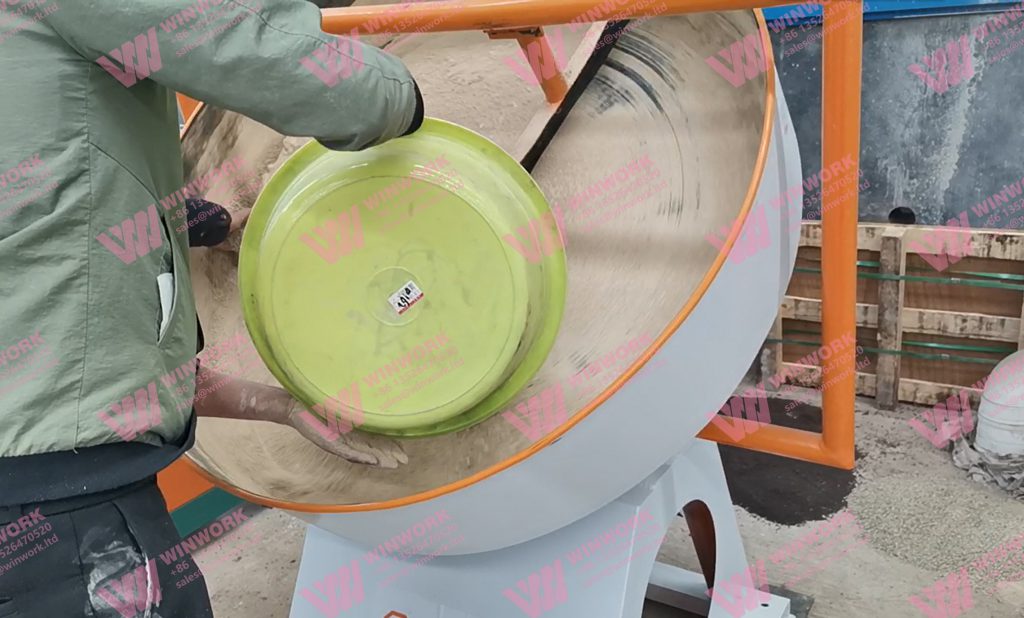
Bentonite Cat Litter Disc Granulator
Get A Quote