In modern agriculture, the demand for high-quality fertilizers continues to grow. Among the various types of fertilizers, NPK (Nitrogen, Phosphorus, and Potassium) fertilizers play a crucial role in improving soil fertility and crop yields. The production of NPK fertilizers requires advanced granulation technology to ensure uniformity, efficiency, and cost-effectiveness, such as Rotary drum granulator for NPK fertilizers.
One of the most widely used granulation machines in NPK fertilizer production is the rotary drum granulator. This equipment is designed to process large quantities of raw materials into high-strength, uniform granules. This article explores the working principle, advantages, features, and selection criteria for a rotary drum granulator for NPK fertilizers, providing insights into its role in large-scale fertilizer production.
1. Understanding the Rotary Drum Granulator for NPK Fertilizers
A Rotary drum granulator for NPK fertilizers is a type of fertilizer processing equipment that utilizes rotating motion to convert powdered or semi-liquid raw materials into solid granules. This process involves a combination of rolling, tumbling, and the application of binding agents to ensure granule formation.
The granulation process in NPK fertilizer production includes:
-
Raw Material Input: The NPK components are fed into the granulator, typically including ammonium phosphate, urea, potassium chloride, and other additives.
-
Moisture Addition & Binding: A liquid binder (water, steam, or chemical additives) is sprayed into the rotating drum to facilitate granulation.
-
Granule Formation: As the drum rotates, the particles stick together, forming small granules that grow in size through layering.
-
Drying & Hardening: The formed granules are transferred to a drying system to remove excess moisture and strengthen their structure.
-
Screening & Packaging: The final product is screened for size consistency before being packaged for distribution.
This process ensures high efficiency, minimal material waste, and uniform granule size—essential factors for high-quality NPK fertilizers.
2. Advantages of Using a Rotary Drum Granulator for NPK Fertilizers
A Rotary drum granulator for NPK fertilizers provides several benefits that make it the preferred choice for large-scale fertilizer manufacturers:
✔ High Granulation Rate – Achieves a granulation efficiency of up to 90%, ensuring minimal raw material loss.
✔ Uniform Granule Size – Produces consistent granules, improving fertilizer quality and application efficiency.
✔ Continuous & High-Capacity Production – Capable of processing 5 to 30 tons per hour, making it ideal for large-scale operations.
✔ Energy & Cost Efficiency – Uses a low-power consumption design, reducing operational costs.
✔ Durability & Long Lifespan – Constructed from corrosion-resistant and wear-resistant materials, ensuring a long service life.
✔ Versatility – Compatible with different NPK fertilizer formulas, including compound fertilizers, organic-inorganic blends, and slow-release fertilizers.
3. Key Features of a High-Performance Rotary Drum Granulator
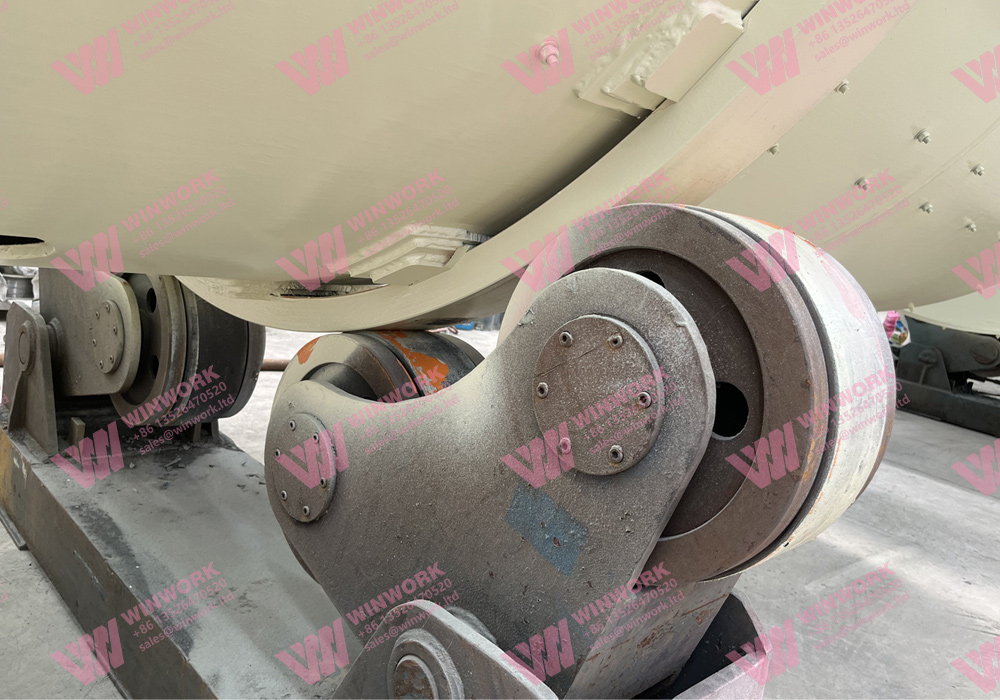
Rotary drum granulator rollers
When choosing a rotary drum granulator for NPK fertilizer production, it’s essential to look for the following features:
✔ High-Strength Cylinder: Made of stainless steel or anti-corrosion alloy to withstand harsh materials.
✔ Optimized Rotation Speed: Ensures efficient granulation while preventing excessive dust formation.
✔ Integrated Steam & Moisture Control System: Provides consistent binding for strong granules.
✔ Adjustable Inclination Angle: Enhances material movement and improves granulation efficiency.
✔ Large Capacity Output: Supports large-scale production without frequent maintenance interruptions.
✔ Automatic Control System: Monitors and adjusts granulation parameters in real time, reducing manual intervention.
Investing in a high-quality rotary drum granulator ensures greater efficiency and reliability in NPK fertilizer production.
4. Factors to Consider When Selecting a Rotary Drum Granulator
Choosing the right rotary drum granulator for NPK fertilizers requires careful consideration of several factors:
4.1 Production Capacity
-
Select a granulator that meets your output requirements, whether it’s 5 TPH (tons per hour) or 30 TPH.
-
Ensure it can handle fluctuations in production demand without efficiency loss.
4.2 Granule Size Requirements
-
The ideal granule size for NPK fertilizers typically ranges between 2-5 mm.
-
Some machines offer adjustable settings for customizing granule size.
4.3 Raw Material Compatibility
-
The granulator should work with various NPK raw materials, including urea, ammonium sulfate, superphosphate, and potassium chloride.
4.4 Material Durability & Maintenance Needs
-
Look for anti-corrosion coatings and wear-resistant parts to extend the equipment’s lifespan.
-
Choose a model with easy-to-replace components to minimize downtime during maintenance.
4.5 Energy Efficiency & Environmental Compliance
-
Opt for models that feature low power consumption to reduce operating costs.
-
Ensure compliance with environmental regulations to minimize dust and emissions.
5. Comparison: Rotary Drum Granulator vs. Other Granulation Methods
A rotary drum granulator is one of several granulation methods available. Below is a comparison with other common granulation techniques:
Feature | Rotary Drum Granulator | Disc Granulator | Extrusion Granulator |
---|---|---|---|
Production Capacity | High (5-30 TPH) | Medium (1-10 TPH) | Low (0.5-5 TPH) |
Granule Uniformity | Excellent | Moderate | Good |
Automation Level | High | Medium | Low |
Raw Material Adaptability | Versatile | Limited | Very Limited |
Energy Consumption | Moderate | Low | Low |
Cost Efficiency | High | Medium | Low |
From this table, it is clear that rotary drum granulators are the best choice for high-capacity NPK fertilizer production, offering superior efficiency and uniformity.
6. Future Trends in Rotary Drum Granulation Technology
As fertilizer production technology advances, rotary drum granulator for NPK fertilizers are evolving with new innovations:
📌 AI-Powered Monitoring Systems – Real-time tracking of granulation performance for enhanced efficiency.
📌 Energy-Efficient Designs – Optimized heating and cooling systems to reduce fuel and electricity consumption.
📌 Eco-Friendly Materials – Development of low-emission and sustainable fertilizer granulation processes.
📌 Customizable Granulation Options – Machines with flexible designs for multiple fertilizer types.
By investing in modern rotary drum granulator for NPK fertilizers, manufacturers can boost efficiency while minimizing environmental impact.
Conclusion
A rotary drum granulator for NPK fertilizers is a critical piece of equipment in high-volume fertilizer production. With high efficiency, uniform granule size, and cost-effective operation, it remains the best choice for large-scale NPK fertilizer manufacturing. By selecting the right machine with advanced features, manufacturers can optimize productivity, reduce costs, and maintain high product quality.
If you are looking for a reliable rotary drum granulator for NPK fertilizer production, investing in the right model ensures long-term profitability and sustainability in the fertilizer industry.
Get A Quote