Urea compound fertilizer is one of the most widely used fertilizers in modern agriculture due to its high nitrogen content and efficient performance in promoting plant growth. The urea compound fertilizer production line is designed to produce fertilizers by combining urea with other essential nutrients such as phosphorus and potassium, creating a balanced nutrient mix for crops. This production line is a key component in large-scale fertilizer manufacturing and is used extensively in the agricultural sector.
What is Urea Compound Fertilizer?
Urea (NH₂CONH₂) is a nitrogenous fertilizer that is widely used for providing nitrogen, a key nutrient for plant growth. Urea compound fertilizers combine urea with other nutrients such as phosphates (P) and potash (K) to create a more balanced fertilizer that promotes overall plant health. These fertilizers are designed to provide crops with the full range of nutrients they need for optimal growth, including:
- Nitrogen (N): Encourages robust vegetative growth.
- Phosphorus (P): Promotes root development and flowering.
- Potassium (K): Helps plants resist diseases and improve water absorption.
The use of urea in compound fertilizers ensures a high nitrogen content, making it ideal for fast-growing crops that require large amounts of nitrogen.
Stages in the Urea Compound Fertilizer Production Line
A urea compound fertilizer production line involves several stages, each essential to the creation of high-quality fertilizer. Below are the key stages in the production process:
a. Raw Material Preparation
The first step in the production process is the preparation of raw materials. The primary raw materials for producing urea compound fertilizer are:
- Urea: The main source of nitrogen.
- Phosphates: Typically, superphosphate or ammonium phosphate is used.
- Potassium salts: Such as potassium chloride or potassium sulfate.
- Other additives: Including sulfur, trace elements, and micronutrients that may be required for specific crop needs.
At this stage, the raw materials are carefully measured to ensure that the correct nutrient balance is achieved in the final product.
b. Granulation Process
The granulation process is crucial for producing uniform-sized fertilizer particles. There are different types of granulation methods, including:
- Wet Granulation: Involves mixing the raw materials with water and then using a granulator to form spherical pellets. The process is often followed by drying and cooling.
- Dry Granulation: In this method, the raw materials are mixed and compressed into granules without the use of water. The granules are then screened for size uniformity.
The choice of granulation method depends on the type of fertilizer being produced and the desired final product characteristics.
c. Granule Drying and Cooling
After the granulation process, the wet fertilizer granules are sent to a dryer. The purpose of the drying process is to reduce the moisture content of the granules, ensuring that they remain stable during storage and transportation.
Once dried, the granules are then cooled to prevent clumping. Coolers are used to lower the temperature of the granules, ensuring that they are easy to handle and store.
d. Screening and Coating
Once the fertilizer granules are dried and cooled, they are sent through a screening machine to ensure uniform size and remove any oversized or undersized particles. The uniformity of granule size is critical to ensure even distribution when the fertilizer is applied.
Some urea compound fertilizers are coated with anti-caking agents to prevent the granules from sticking together, especially under humid conditions. This step helps maintain the fertilizer’s quality during storage and use.
e. Packaging and Storage
After screening, the finished urea compound fertilizer is ready for packaging. The fertilizer is packed into bags or bulk containers for transportation to farmers. At this stage, the fertilizer may be labeled with relevant information about the nutrient composition, dosage instructions, and safety precautions.
Technology in the Urea Compound Fertilizer Production Line
Modern urea compound fertilizer production lines are equipped with advanced technology to ensure high-quality products and efficient production processes. Some key technologies involved in the production line include:
a. Automatic Control Systems
Advanced PLC (Programmable Logic Control) systems are used to monitor and control the entire production process. These systems ensure that the right quantities of raw materials are mixed, the granulation process is controlled, and the drying and cooling processes are optimized. The use of automatic systems helps maintain consistency and quality in the final product.
b. Energy-efficient Dryers and Coolers
Energy-efficient rotary dryers and cooling systems help reduce energy consumption during the drying and cooling stages. These systems are designed to minimize heat loss and ensure the efficient processing of the fertilizer granules.
c. Granulation Technology
Modern granulators are designed to produce high-quality, uniform-sized granules. The use of advanced disc granulators or drum granulators ensures that the urea compound fertilizer has the desired particle size, enhancing its performance in the field.
Advantages of Urea Compound Fertilizer
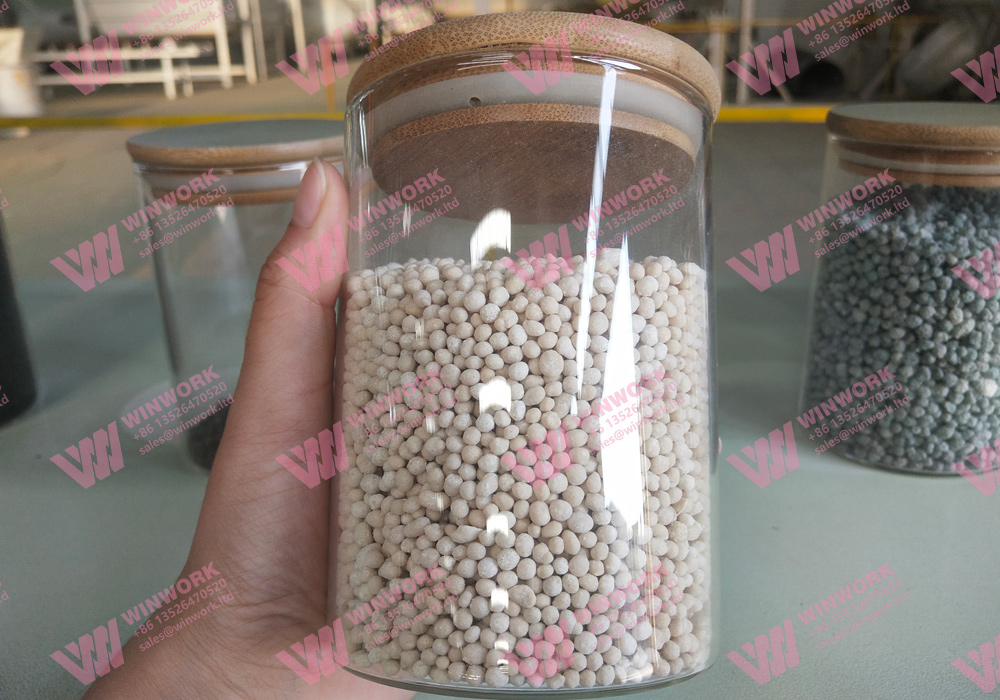
Rotary drum granulator finished granules
Using a urea compound fertilizer offers several advantages over single-nutrient fertilizers:
- Balanced Nutrition: Urea compound fertilizers provide a balanced mix of essential nutrients (NPK), reducing the need for multiple fertilizers and improving the overall health of the soil.
- Improved Crop Yield: By supplying the full range of nutrients, urea compound fertilizers promote better growth, higher crop yields, and better resistance to pests and diseases.
- Better Nutrient Efficiency: Urea compound fertilizers are formulated to ensure that nutrients are available to plants in the correct proportions, reducing nutrient wastage.
- Cost-effective: By combining multiple nutrients into one product, urea compound fertilizers simplify the application process and reduce labor costs.
Conclusion
The urea compound fertilizer production line is a highly efficient and advanced process that combines urea with other essential nutrients to create high-quality fertilizers. By optimizing the production stages, including raw material preparation, granulation, drying, cooling, and screening, manufacturers can produce fertilizers that promote robust plant growth, improve soil fertility, and increase crop yields. With the use of advanced technology and efficient machinery, the urea compound fertilizer production line helps ensure that fertilizers meet the specific nutrient needs of crops, leading to sustainable agricultural practices.
Get A Quote